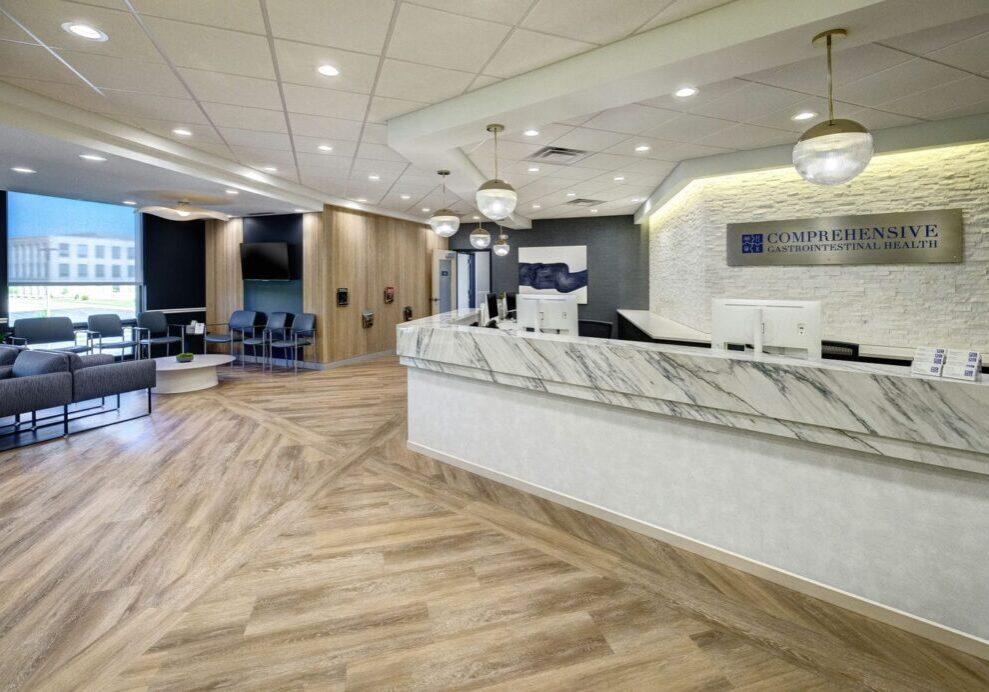
If you’re considering or are in the process of building a healthcare facility, you know too well that the design, construction and build process requires a major investment. In an industry where cutting corners and compromising quality and compliance are not options, you have to find safer, more effective ways to save money.
Access to innovative construction techniques and materials can lead to significant cost savings. Let’s explore the latest cost-effective construction advancements designed to maintain the quality and safety of your healthcare facility.
Prefabrication
Prefabrication saves money by cutting down on transportation, weather related delays and labor costs. The work is performed at the factory level where key components are created on an assembly line. This contributes to several cost savings including:
- The manufacturer receives price cuts on materials purchased in bulk with those savings past on to the customer
- Work traditionally performed in stages at the job site can be completed simultaneously when using prefabricated components, speeding up the construction process
- The prefabrication process takes place indoors, eliminating weather-related costs including delays and material/construction damage
- Transportation costs are also often reduced as materials usually delivered separately such as cladding, millwork, substrates, etc. are delivered assembled directly from the manufacturer
The final prefabricated pieces are delivered to your medical facility site where they are quickly assembled. Apps used in the prefabrication process can also facilitate change order efficiency to help reduce costs.
Modular Designs
Modular designs are based on a plug and play configuration making them more flexible and efficient. This building method reduces installation and renovation costs such as tearing out walls to access mechanical, plumbing, and electrical services. Modular construction is a turnkey solution applied to both exterior and interior facility components. Depending on the scope of your project, using modular components can complete some projects within a few weeks.
You also experience long-term cost savings because modular components are reusable. As a result, they can be removed and relocated based on your facility’s needs. Modular components are ideal for space adjustments allowing you to expand or shrink departments, workspaces, or patient care rooms based on changing demand. As a result, your facility remains scalable with smaller investment required.
Lean Construction Practices
Lean construction is a method focused on reducing waste throughout the construction process. Reduced waste applies to time, resources, processes, and materials which all save money through constantly improving efficiency and smarter use of resources.
Lean methodologies are applied both prior to and during construction to improve processes and streamline all aspects of your project’s progress. The team continues to focus on the 5-S system which includes:
- Sort: This works like a decluttering process removing anything not required at the site including tools, materials, and equipment. The goal is to improve efficiency and optimize space. This could mean moving certain items to other workspaces where they make more sense.
- Set in Order: The remaining items are sorted and placed in a logical location based on how often they are used, who uses them and whether certain tools always used together should be grouped.
- Shine: This stage ensures the site always remains clean and organized with tools and materials stored or placed in the appropriate spot. Messes are kept to a minimum to improve efficiency and safety.
- Standardize: Once the above steps are complete the project is standardized to ensure order is maintained. This step also puts systems in place to standardize procedures, instructions, tasks, scheduling, etc. to maintain efficiency and reduce mistakes and wasted time.
- Sustain: The biggest challenge is sustaining order and newfound efficiencies. The idea is to constantly identify opportunities for improvement and introduce new efficiencies. By sustaining standardized procedures, the project maintains order to see the most positive results and ongoing waste reduction.
The lean method combined with the 5-S system ensures the construction site reduces waste, remains efficient, and improves safety to limit damage and injuries. Integrated delivery methods are also critical to lean methods. Which means hiring a single team specializing in all aspects of design, architecture, and construction helps you:
- Minimize risk
- Maintain efficient timelines
- Reduces waste
- Maximize your budget
- Improve return on investment
Maximizing Your Budget with a Proven Process
As a medical facility build expert, APEX uses architectural and design techniques aligned with your budget using lean methods and construction innovations suited to your needs. We believe in proactive management that addresses your cost challenges.
Lean and industry best practices allow us to relentlessly improve efficiencies through our keen understanding of project timelines and costs. As a result, we avoid project delays and address budget issues with ongoing solutions that keep your project on track. Our proven process leverages construction techniques and innovations designed to improve efficiency and bring more value to our clients.
Embrace innovative healthcare facility designs with Apex.
Your healthcare facility can become scalable and sustainable with flexible designs that incorporate forward-thinking planning. Apex Design Build creates expandable, adaptable designs for longevity and ongoing cost-effectiveness. Reach out to Apex if you’re considering a medical facility design and build project.